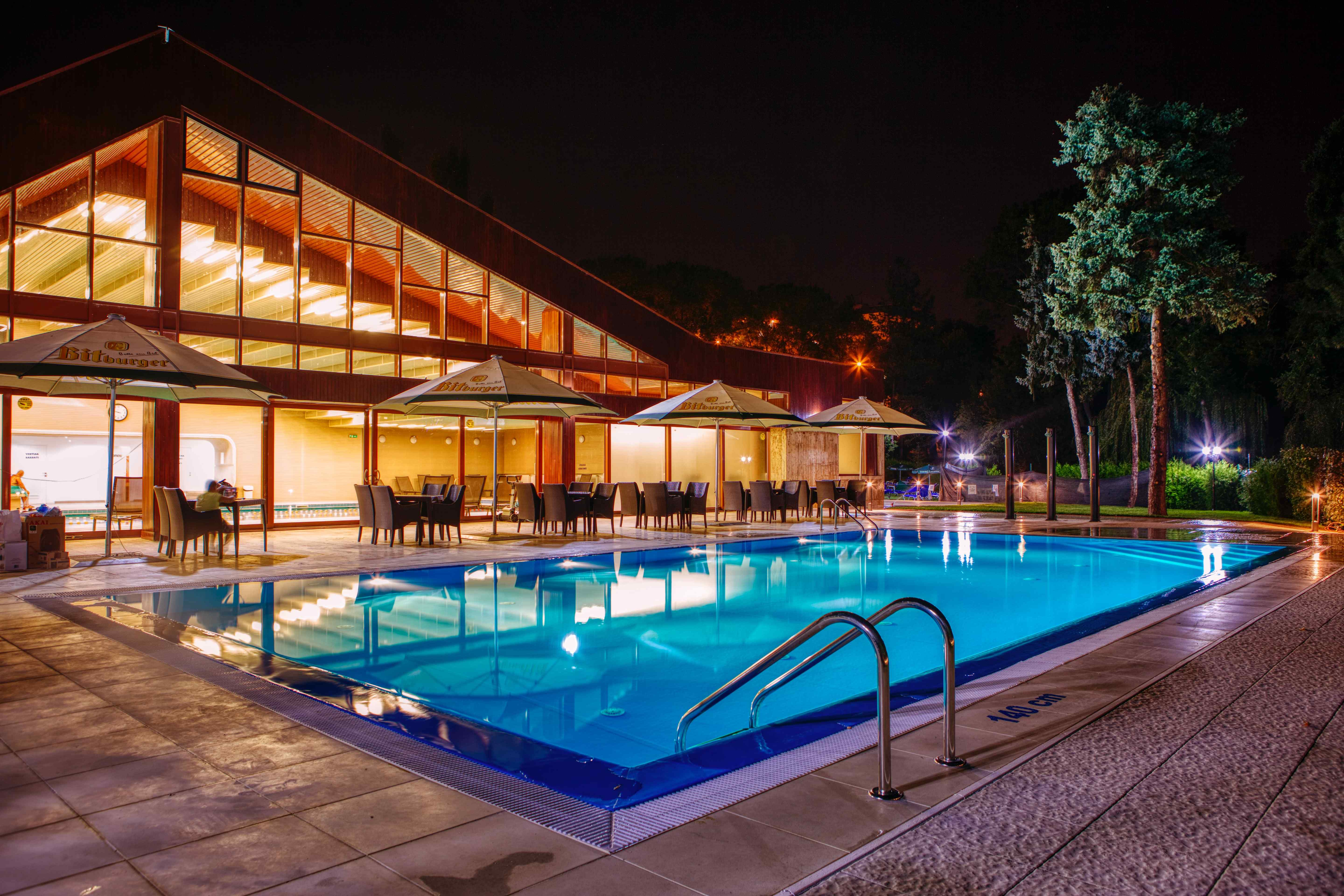
Here’s Why Allied Cycles Moved Production to Asia
With their latest two bikes, the updated BC40 mountain bike and Able gravel bike, Allied Cycles made it known that they were no longer making those models in the USA.
Turns out, they’ve moved ALL frame production for EVERY model there, saying it was necessary to give them the growth capacity to meet demand.
While current (as of this post going live in May 2025) tariffs on Chinese-made goods may make that decision financially questionable, the reality is that many factories in Asia make excellent bikes. Simply put, that’s where the bulk of the carbon fiber bicycle manufacturing expertise is, particularly for mass production. And, to be fair, shifting production there is something they’ve been working on for more than a year.
If you’d like to hear it in their words, I visited their HQ in Arkansas for an updated tour, check it out:
PlayCheck out my prior factory tour to see how they were making the bikes near Bentonville, AR. If you prefer pics and paraphrasing, here are my thoughts and photos from the visit…
The short of it is this: Allied Cycles used to design, engineer, test, manufacture, finish, paint, assemble, and ship their bikes from Rogers, Arkansas, near Bentonville.
Now, they design, engineer, test, finish, paint, assemble, and ship their bikes in Rogers, Arkansas. The only thing missing from the original list is the manufacturing, and even that’s not 100% true.

They’re still machining the alloy parts like linkages, stems, and other bits in house. These get installed during assembly.
From a design standpoint, Allied’s CEO, Drew Medlock, says that they’re still doing all initial design, prototyping, and testing 100% in house. But now they’re also able to tap into the manufacturing expertise at the foreign factory when finalizing the layup, combining brainpower to yield a better final product.


Now, the raw carbon frames are made in China, then shipped back to Allied’s HQ for inspection. For now, every single frame is checked for tolerances, with every port, hole, thread, and component attachment point physically checked with pass/fail measurement tools. Every frame is weighed, too.
They’re also inspected for blemishes and other cosmetic and structural issues, then accepted or rejected.


From there, they move onto sanding to prep the frame for paint (back right station).
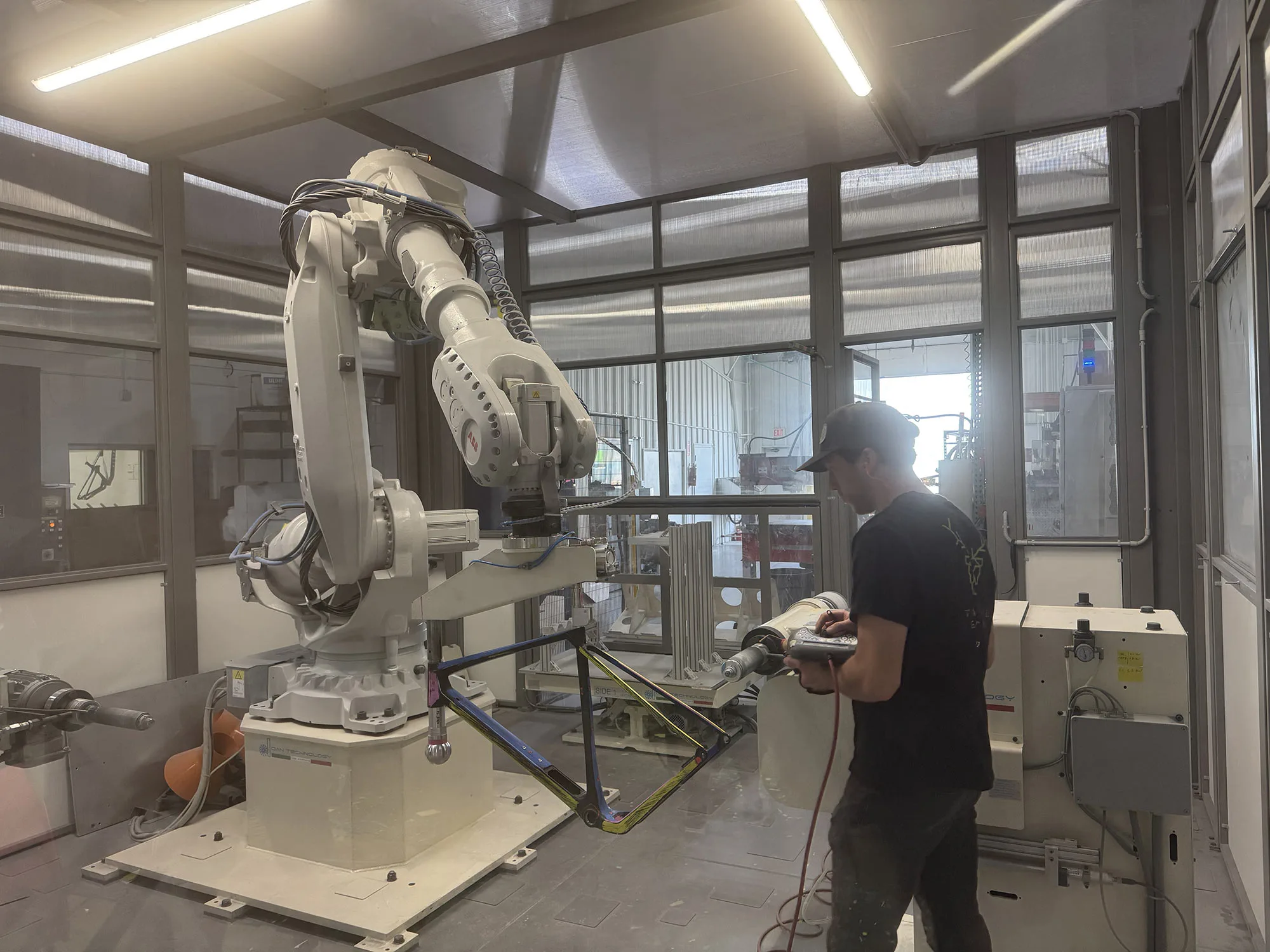
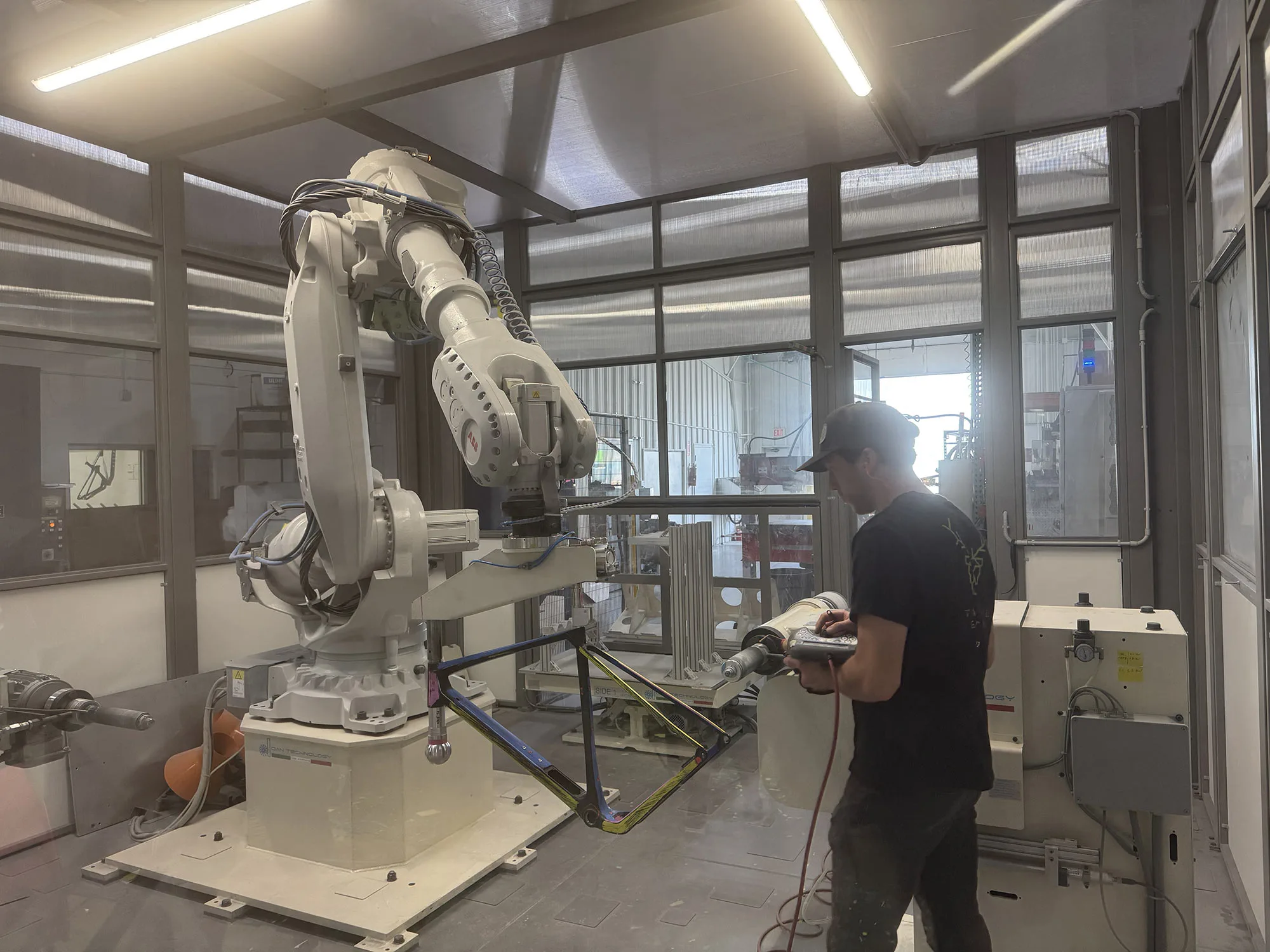
They’re still using their robot to sand the bikes. In this pic (above), the color-coded sections on the frame represent a different sanding tool inside the room, and they’re training it on the new Able. Each frame and frame size needs its own program, then, the robot can smooth most of the frame to prep it for paint.
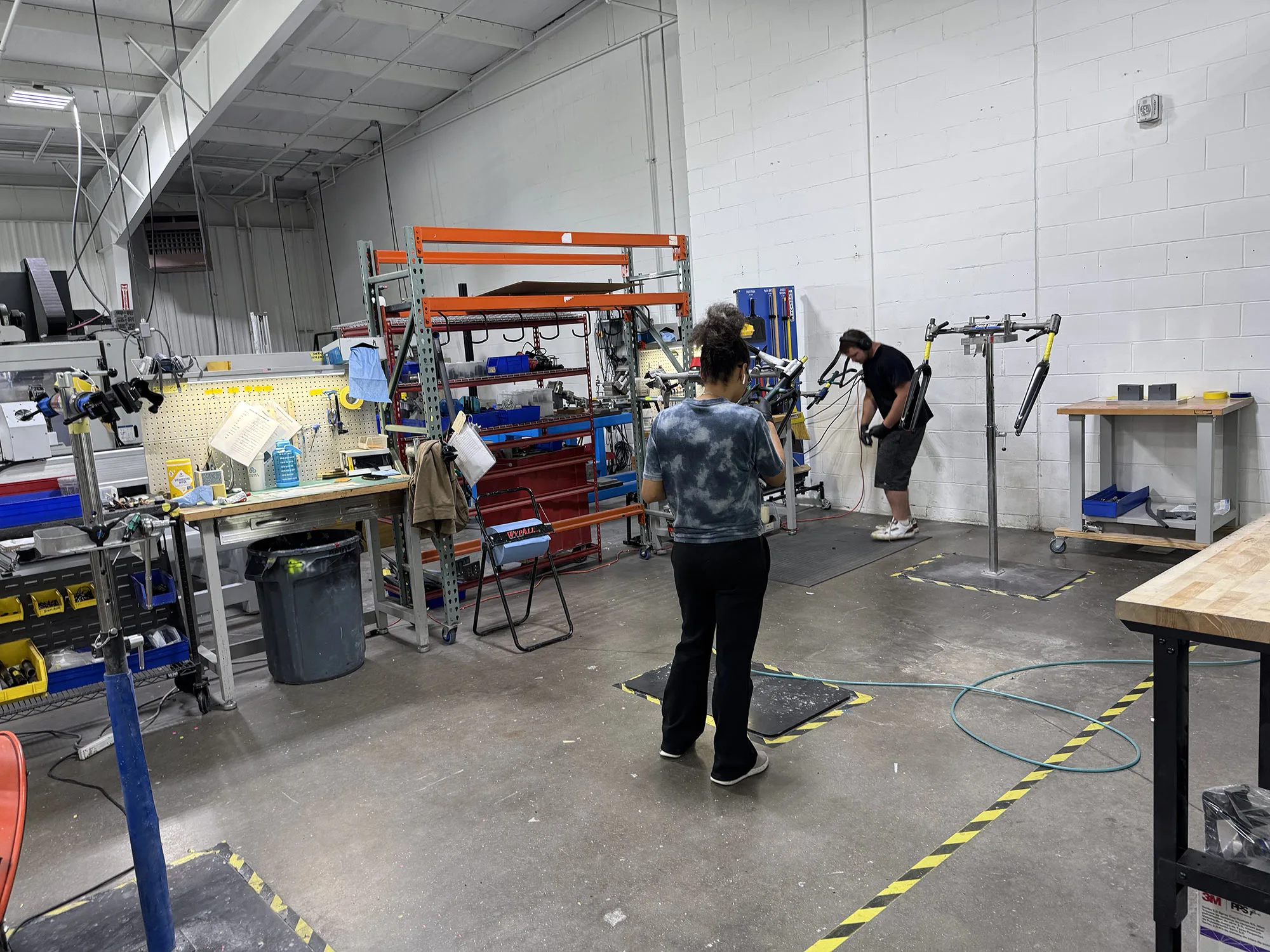
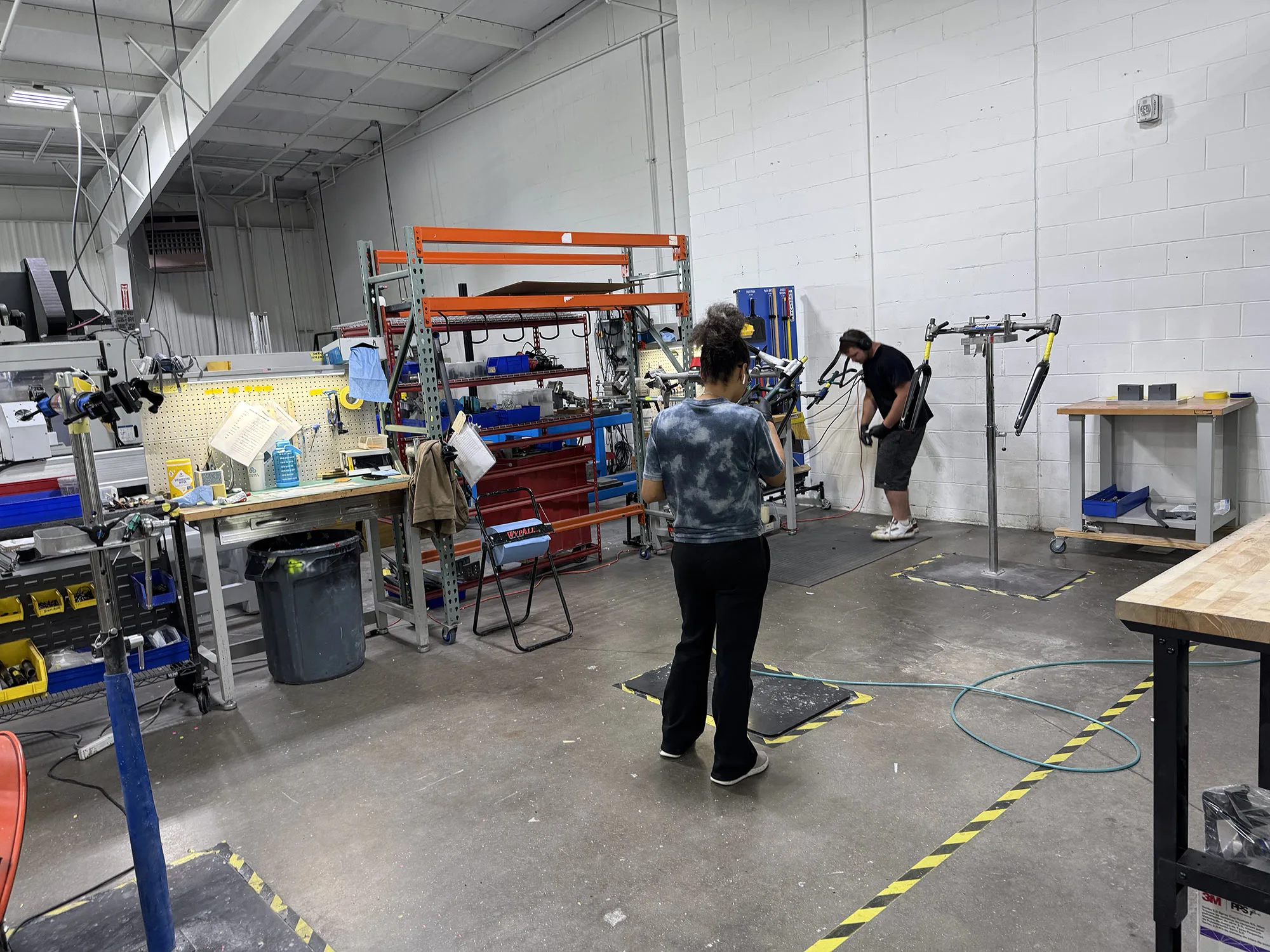
The frames are painted, with any masking done to create the painted logos. You can also opt for shiny foil logos, which are decals that will go under a final clear coat to protect them.


After painting, they’re racked and inspected again.
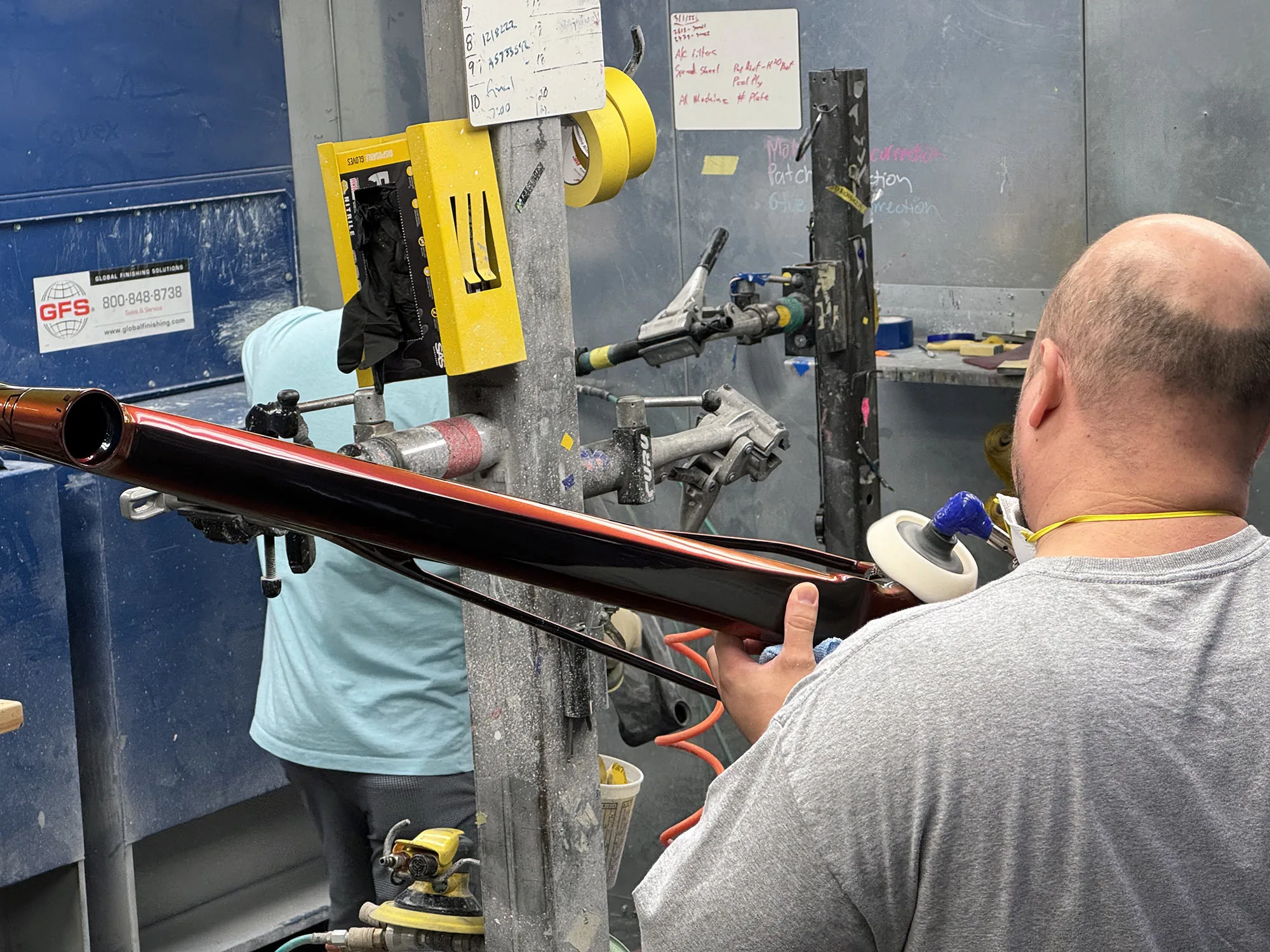
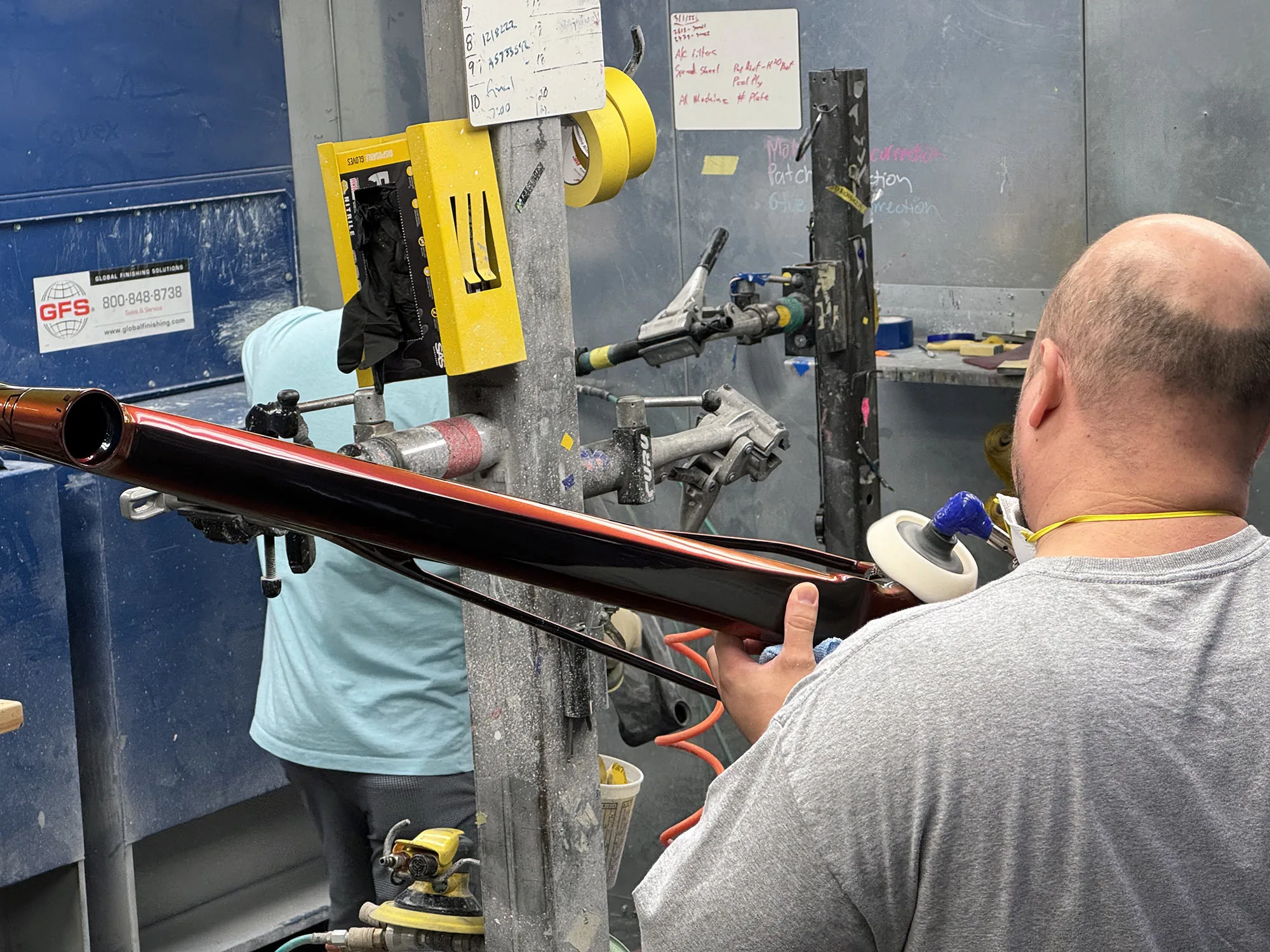
If any blemishes are found, they get wet sanded and polished as needed to yield a perfect paint finish before moving to prep and assembly.
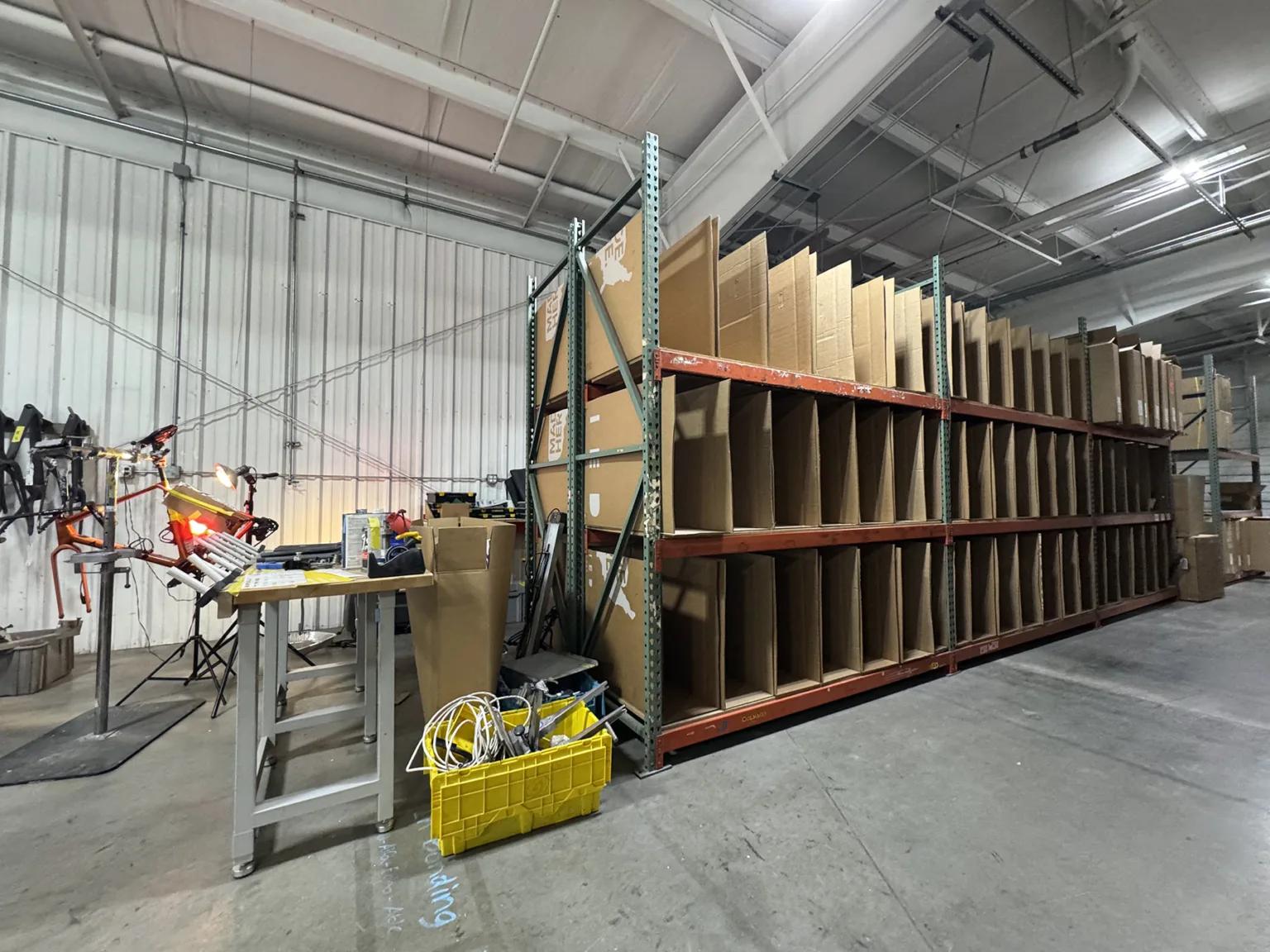
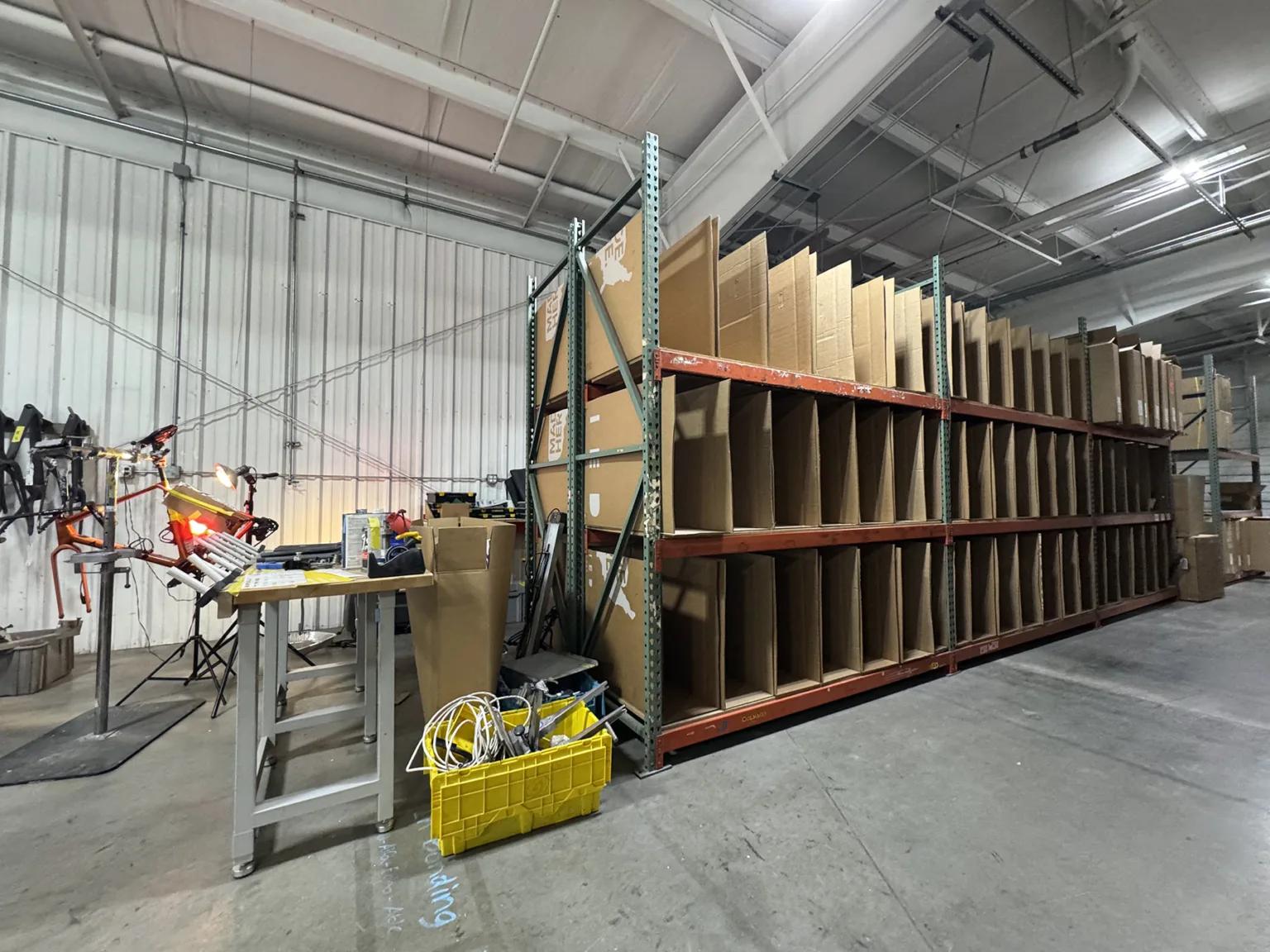


Inspected frames get slotted until they’re ready for the next stage. All components are racked and ready for pulling, with each bike getting its own build sheet and cart. Each cart has a bin for every component, so they know when everything’s there and ready for assembly when all of the bins are full.
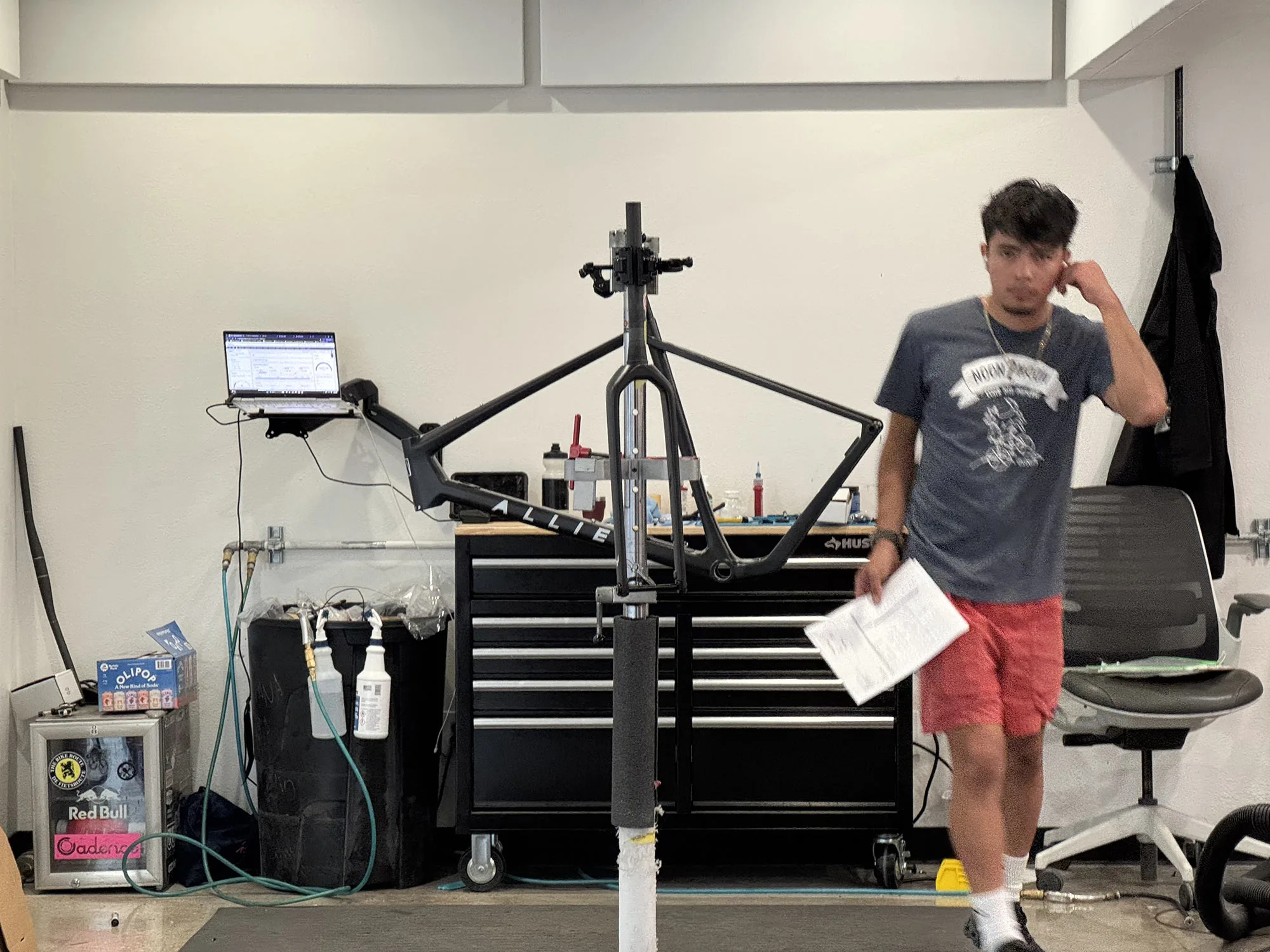
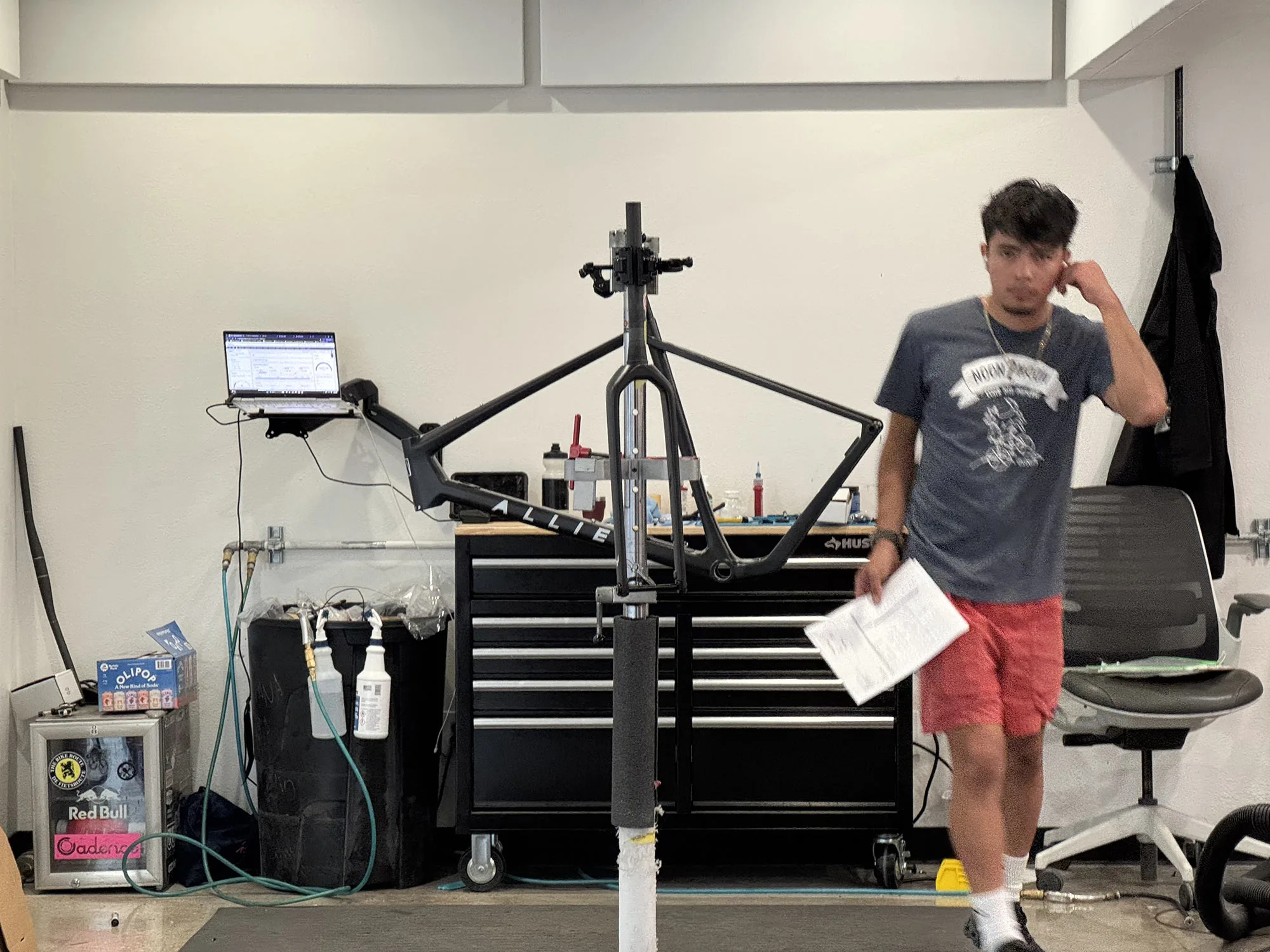
Every bike is assembled to order, so you can pick and choose your drivetrain, wheel, tire, and cockpit spec. Every bike is also painted to order, letting you completely customize the bike, just like before.
Allied Cycles’ Duet Bar & Stem

For now, they’re making their Duet carbon handlebar in-house. And they’re continuing to make the alloy stem in-house, along with suspension linkages and other small parts. This lets them make custom stem angles and lengths for their sponsored athletes like Kate Courtney and Payson McElveen.
The Duet is sold only as a combo, and it’s insanely light, with a bar plus stem coming in as light as 200g… for the pair! That’s lighter than most one-piece bar+stem combos on the market, and it offers full adjustability and stem length options.


Their secret is a unique stem design that fully envelops the handlebar in the face, with only a single clamping section at the bottom. And that clamping section is unique in that it dips down, away from the bar, to remove any pressure points or sharp edges against the carbon.
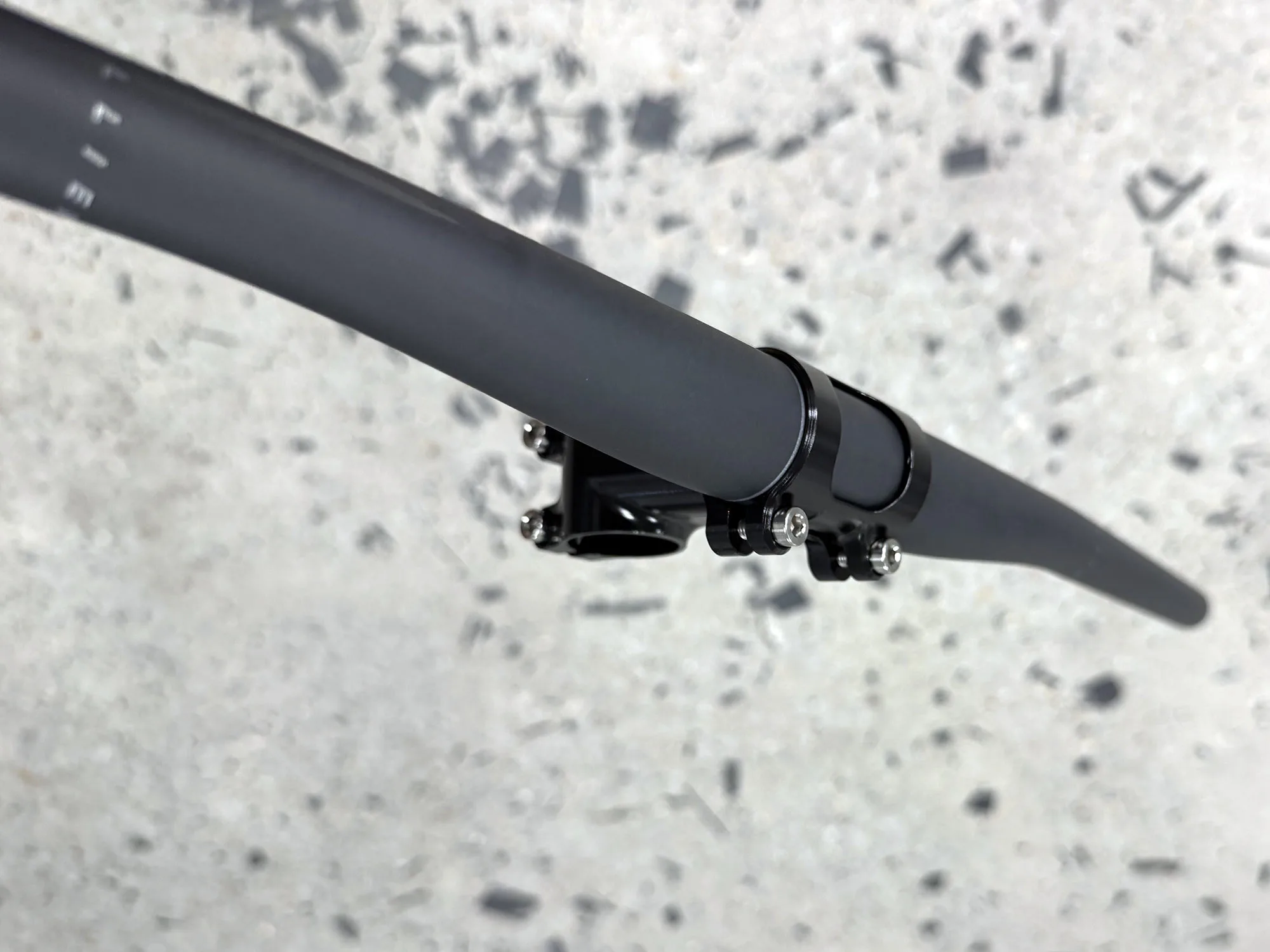
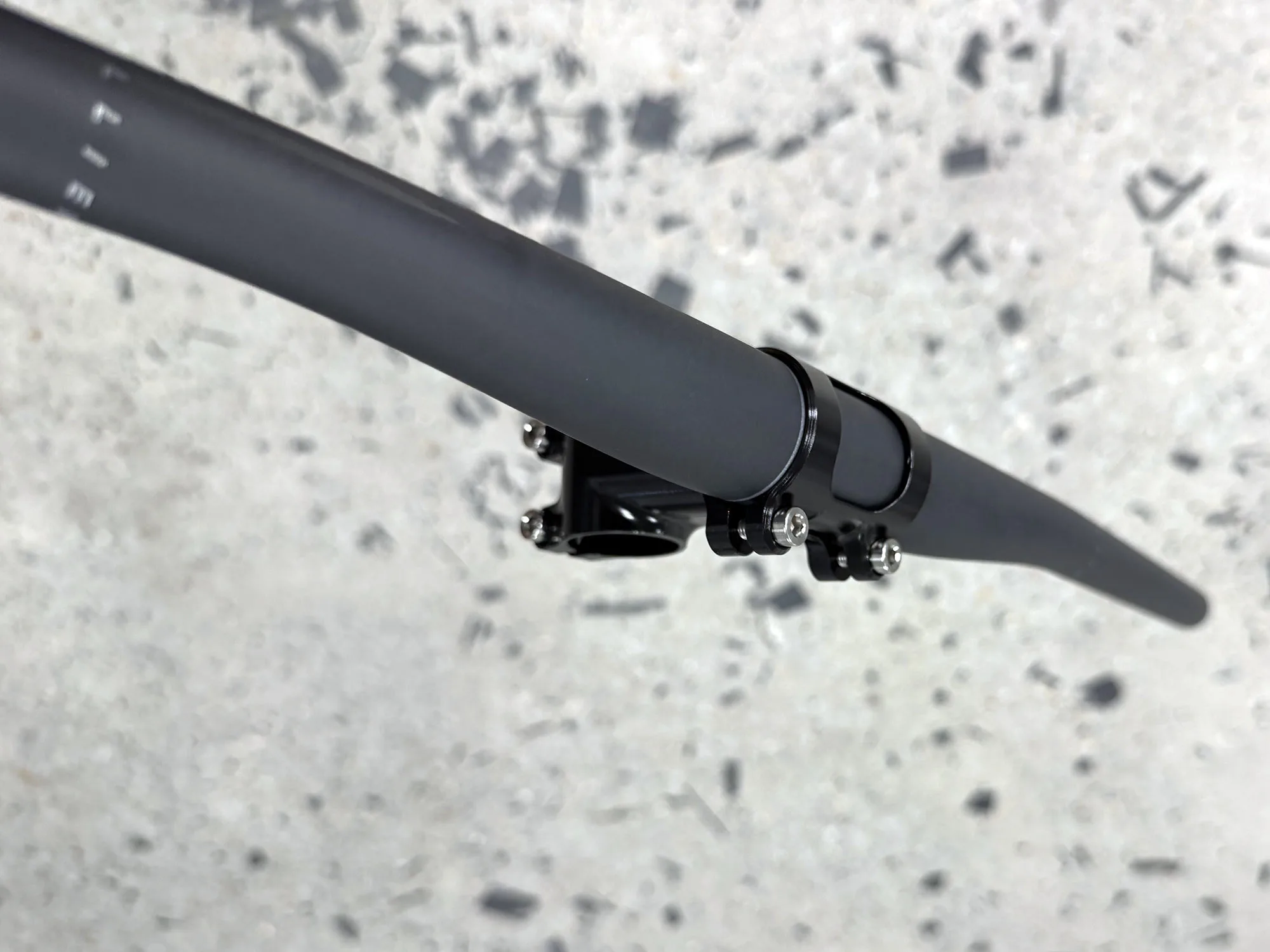
That lets them reduce the amount of carbon fiber used in the center section, which they say isn’t necessary to reinforce the bar since they’re not using a standard stem that clamps from front and back… something they verified with FEA.


Another cool feature is the integrated cycling computer mounting bolts on the top, so you don’t need to clamp that around the bar, either. It’s available separately for $325 with a computer mount included (choose Garmin or Wahoo…but you can rotate to switch).
AlliedCycleWorks.com
ES by OMG
Euro-Savings.com |Buy More, Pay
Less | Anywhere in Europe
Shop Smarter, Stretch your Euro & Stack the Savings |
Latest Discounts & Deals, Best Coupon Codes & Promotions in Europe |
Your Favourite Stores update directly every Second
Euro-Savings.com or ES lets you buy more and pay less anywhere in Europe. Shop Smarter on ES Today. Sign-up to receive Latest Discounts, Deals, Coupon Codes & Promotions. With Direct Brand Updates every second, ES is Every Shopper’s Dream come true! Stretch your dollar now with ES. Start saving today!
Originally posted on: https://bikerumor.com/heres-why-allied-cycles-moved-production-to-asia/